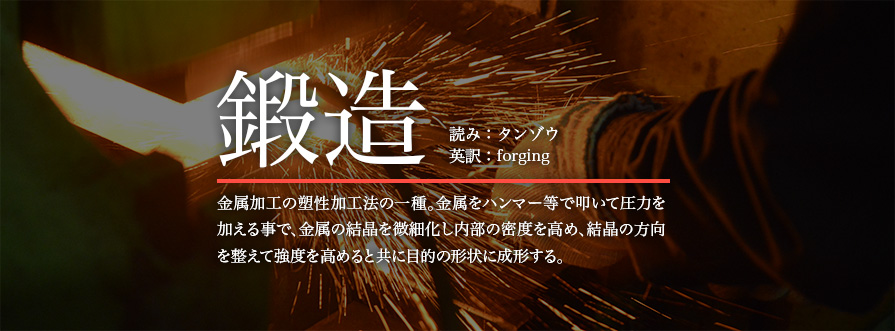
熱間型打ち鍛造は強度・精度・コストダウンを兼ね備えた合理的製造法
熱間型打ち鍛造は、金属素材を高温に加熱して成形する塑性加工法です。
生成された金属素材には、内部組織(結晶粒)にバラツキがあります。
この金属素材を再結晶温度以上の高温(鉄の場合、一般には1100~1250℃)に加熱して打撃や加圧することで、内部の空隙をつぶし緻密で均質な組織となるため、硬さ・引張り強度など機械的性質が高まります。
それと同時に目的の形状に成形されるので、機械加工を省いたり最小限の加工で済み、材料の節約にもなり、大変合理的でコストダウンにつながる製造方法と言えます。
鉄は熱いうちに打て…と昔から言われる通り、高温で軟化した金属素材は、比較的小さな力で変形させる事ができます。
小さな力と言っても、昔のように鍛冶職人が金槌で叩いている訳ではありません。熱間型打ち鍛造では部品の形状などに合わせて様々な装置が利用されます。
主にエアードロップハンマーやプレスが用いられます。当社では2台のエアードロップハンマー(1/3tと1t)を使用し,小物鍛造を得意としています。エアードロップハンマーは,空気の圧力でラムを上昇、下降させることで、熱せられた金属を鍛えます。このとき、ラムの先端に 金型(上)と、叩きつける台に金型(下)を取りつけ、間に加熱した材料を置いて打撃することで金型に彫込んだ形状の部品を作るのです。
ハンマーで鍛錬することで生まれる、メタルフロー(鍛流線)
メタルフロー(鍛流線)とは
鍛造の強靭性を象徴しているのが製品の断面に現れるメタルフロー(鍛流線)です。
樹木には年輪があるように鍛造品には製品形状に沿ったメタルフローが形成されるため、高い強度・耐久性・衝撃値などが得られ、安全性を必要とする重要な部品に使用されています。
鍛造品 | 鋼材からの削り出し品 | 鋳造品 | |
---|---|---|---|
組織形状図 | ![]() |
![]() |
![]() |
組織 | 材料形状に沿ってメタルフローが流れている | 加工した部分でメタルフローが切断されている | メタルフローなし |
性質 | 反復曲げ応力に強い | 反復曲げ応力に弱い | 反復曲げ応力に弱い |
このような性質から、熱間鍛造は歯車の他プロペラシャフト、クランクシャフト、ステアリング部品など、高強度・複雑形状部品に多く用いられます。
熱間型打ち鍛造のメリットをまとめると、次のようになります。
- ハンマーで叩くことで金属の内部組織が密となり、内部欠陥がなくなる
- 製品形状に合ったメタルフローができることで強度・靱性が向上する
- 製品の最終寸法に近い形状で成形されるので切削工程が削減できる
- 金属を熱してからハンマーで鍛造するので、比較的に小さな力で加工でき、複雑形状部品の製造が可能
- 同一形状のものを小ロットから大量生産まで対応できる
- 他の鍛造方法(冷間・温間)に比べ自由度が高いため少量多品種に対応でき、また材料ロスが少ないためコストダウンに貢献
こうして作られた製品に 熱処理(調質)を加える事で、硬度調整を行ったり、旋盤加工、フライス加工、ドリル孔加工、塗装処理、磨き処理などを行い、お客様の希望される形状で製品を納品しております。
更に合理的な製造をするために冷間コイニングも併用します
熱間鍛造後に寸法精度を上げたり、表面にコインのように模様を成形したりするために常温で行う鍛造のことで圧印加工ともいいます。
弊社で冷間コイニングを行う大きな理由としては以下の3つが挙げられます。
- 寸法精度向上
- 切削加工時の基準面作り
- 切削なし
また良好な表面を得るには圧印前にスケールを落としたり、ショットブラストをかけたりします。なお圧印は低い温度で変形量を小さくして行い、その鍛造品は切削加工を省略したりできるのでコスト的にも有利です。